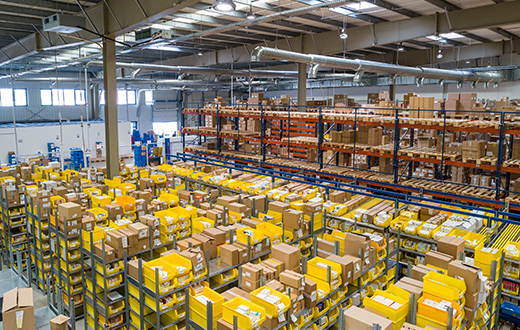
Your warehouse management system is critical to the success of your business, especially if you sell online. Customer satisfaction is determined by your ability to process orders quickly. If your warehouse picker spends too much time going from one location to another, you may not be able to meet your customers' deadlines.
It's critical to invest in a warehouse picking management system that works. Your warehouse's order-picking system can have a significant impact on the efficiency of your supply chain and overall business operations.
What is Order Picking and How Does It Work?
To fulfil a customer order, order picking involves identifying and pulling a product from your warehouse inventory. The product is subsequently packaged and shipped to the consumer. While the procedure appears to be straightforward, it is frequently rather intricate.
It's usually the warehouse's most labour-intensive duty, accounting for up to 55 percent of total warehouse operating expenditures. To guarantee that you're picking things most effectively and productively possible, you'll need to be aware of your alternatives and select the appropriate warehouse picking strategy. Customers' experiences and general satisfaction will improve when you design effective order picking plans and use order picking procedures that are right for your organization - which is critical for developing client loyalty.
Order Picking Systems: An Overview
Order picking systems enable you to swiftly, flexibly, and error-free assemble goods for all orders. They also ensure that your customers' orders are delivered on time.
A good picking system should be durable, efficient, and easy to use and operate. Picking systems in warehouses are based on three fundamental elements:
Picking Technology: Pick-by-Voice, RF, Light, or completely automated employing modern robotics and end-effectors.
The process: Discrete picking, component picking, bulk picking, and wave picking are examples. You must make process decisions on how to incorporate order consolidation and packing in every step.
Order picking and delivery plan: You can either convey the products to the particular order picking associate or the associate can travel to the location of the goods.
According to this, there are three different types of order picking systems:
- Pick to Carton
Before the order choosing process, pick to carton uses the dimensions and weights of the products to select the shipping carton. When done effectively, this method will save you money on supplies, selection, and packing labor, as well as reduce additional handling and improve the buyer's experience.
- Pick to Tote
Pick to Tote allows you to order containers and cartons directly from your computer. This approach delivers the items straight to the operator, reducing the time it takes to obtain the item. When using a pick to tote service, goods-to-person selection becomes extremely efficient. The benefit of having a specialized packing function is that it saves you time and money.
- Pick to Cart
Workers can stroll through the warehouse and pick things off the shelf, place them on a rolling cart, and prepare them for packing and shipping using this warehouse system. This method is best for slow and medium moving items, as well as orders with a low to medium volume. Pick to basket eliminates time-consuming fulfillment stages by allowing batches to be created based on defined criteria. This technique maximizes productivity and saves time by minimizing walking distance based on priority, order size, or order cut-off time.
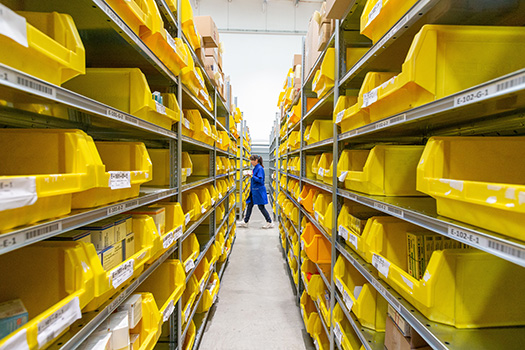
The Most Common Order Picking Methods
There are various sorts of warehouse picking procedures, and not all of them are appropriate for your company. The method you use to pick orders is determined by the size of your warehouse and inventory, the number of employees you have, and the number of customer orders you receive each day.
Examine the following sorts of warehouse order picking methods and select one that will help you manage your supply chain more efficiently and develop your company overall.
- Discreet Picking
Because discrete selection is the most straightforward, it is used by the majority of firms. Picking one order at a time is the approach used in this method. It's straightforward and enables easy monitoring of picker accuracy. It does, however, necessitate more movement than methods that involve picking many orders at once.
- Picking in Groups
This strategy entails picking a batch of orders at a time, one SKU at a time, as the name implies. This method is especially useful when many orders contain the same SKU. In that instance, the warehouse order picker just visits the order pick area for that exact SKU once in order to fulfill multiple customer orders. Batch picking is the most efficient way to reduce travel time and increase production. It's excellent for scenarios when the typical order profile has no more than four SKUs and the SKUs' physical dimensions are minimal.
- Clusters picking
Picking many orders into containers at once is known as cluster picking. The cluster picking method could assist two key piece picking systems:
· Pick-to-cart procedures entail filling a cart with a number of shippers or totes, then having the picking team make a single pass through the picking area, sorting to the pick containers. As a result, they avoid making unnecessary movements.
· The picker sets up the batch of pick containers, which triggers the mechanized picking modules, using Vertical Lift Modules (VLM) that use the independent zone picking method. Following that, the items are sorted into the appropriate select container.
- Wave picking
If you have a lot of different inventory and a high order fulfillment requirement, you should consider wave picking. One picker prepares each order line-by-line in this picking approach.
Rather than merely compiling orders in the order in which they were received, the first review of all orders in order to improve picking and shipping operations. You can ship and construct "waves" of orders throughout the day using this method, sorting them by time and importance.
- Zone-batch picking
Pickers are assigned a zone, similar to standard zone picking, but they are also directed to batch pick within their zone, which is a hybrid of methods. Because zone and batch picking both have a scheduling window, zone-batch picking does as well.
- Zone-wave picking
Pickers are assigned to a zone, and each picker inside that zone picks all of the SKUs for all orders stored in their zone, one order at a time, with one scheduling window for each shift.
- Zone-Batch-Wave picking
The most complicated combination of order choosing techniques. Each picker is assigned a zone and is responsible for picking all SKUs for orders stocked in that zone. Furthermore, the picker selects many SKUs at once, and each shift has various scheduling slots.
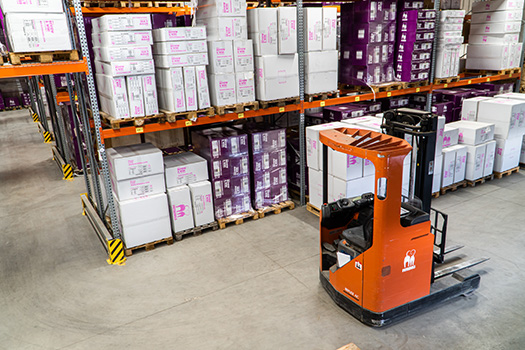
Let's take a look at some of the most common automatic picking methods.
- Pick-to-light
Pick-to-light LEDs and barcode scanners must be installed on racks and shelves throughout the warehouse for this automated picking system to work. The LEDs for SKUs indicated in the order begin to glow after a picker scans a barcode connected to a shipping box (that holds the contents for a single order). Workers retrieve SKUs from their pick list by following these lights.
- Choosing a voice
Pickers receive spoken instructions on what objects to pick and where they are in real-time with voice picking. To speed up the picking process and enhance accuracy, these instructions are communicated through headsets (worn by the pickers) connected to an order management system. Pickers verbally confirm that the picking task is completed once they've finished.
- Picking through a mobile scanner
All items in the warehouse facility must have unique barcodes for mobile scanner-based picking to work. Mobile scanners are used by workers to view pick lists as well as the location of each SKU on the list. Pickers scan each item as it is chosen; if they scan something that isn't on the picklist, the mobile scanner alerts them. This error-detection tool aids in the accuracy of selection. To improve efficiency, warehouse managers might give workers with optimum picking paths.
- Collaborative mobile robots
Robots have become more common in order picking in recent years. Workers used to have to manually collect products from pick lists by pushing their carts from rack to rack and aisle to aisle. Human operators now have access to collaborative mobile robots that can enhance the work of human warehouse associates and automate the transportation of objects throughout the warehouse, thanks to the introduction of collaborative mobile robots. These robots assist in order picking activities by handling the manual task of moving products around. On getting to a pick location, workers retrieve items from their storage location and place them in a bin/container on the robot.
Collaborative mobile robots help minimize walking through real-time route optimization and can be programmed to follow discrete, batch, zone, and cluster picking methods. Collaborative mobile robots also leverage artificial intelligence and machine learning to optimize picking routes and tasks in real-time.
- Vending mechanism picking system
Warehouses are under pressure in today's fast-paced industry to successfully fulfil orders on time. To meet just-in-time order requirements, D&R's order pickup systems offer an efficient and cost-effective option for storing and retrieving layers and cases without a pallet. Fully automated vending mechanism is used in our automated fulfillment systems to choose products from inventory in singles or groups. When the order is accepted from the control system, chosen products are automatically selected and moved to sublines and then to the mainline. which are then palletized and dispatched to the customer.
This solution, cost effective and highly customisable, is extremely proper for small scale warehouses especially of ecommerce business. Picker's labor cost and also picking errors will be minimized.
Summary
Order picking is the core of successful online delivery operations in every profitable e-commerce and retail firm. Order picking is perhaps the most significant function in fulfillment centers, accounting for over 50% of fulfillment center operations and 55% of warehouse operating costs. So, an efficient order picking system is critical. Warehouses utilize a variety of order picking methods to increase productivity and accuracy. Companies should carefully select their order picking system because warehouses that execute order picking activities quickly and accurately are usually the most successful. Modern warehouses with the correct technology benefit from automated warehouse order picking systems.